Configurable apartment homes for urban infill sites

Rapid development

Pre-designed size units

More sustainable

High quality

Less disruption

Mold free

Full control

Bigger scale

Rapid development

Pre-designed size units

More sustainable

High quality

Less disruption

Mold free

Full control

Bigger scale
We provide developers with efficient, high-quality modular apartments for urban infill sites. Combining the efficiency of manufactured housing with the quality and scalability of traditional construction
16
Weeks turnaround from approval to completion
We accelerate your entire development process by 5x with our unique cold-formed steel system.
80%
More accurate cost prediction
Prior to construction, we deliver a digital twin of your building for highly accurate cost & timeline estimation.
35%
Less carbon emission
Our process cuts carbon emissions by an average of 32 tCO2/unit versus traditional construction.
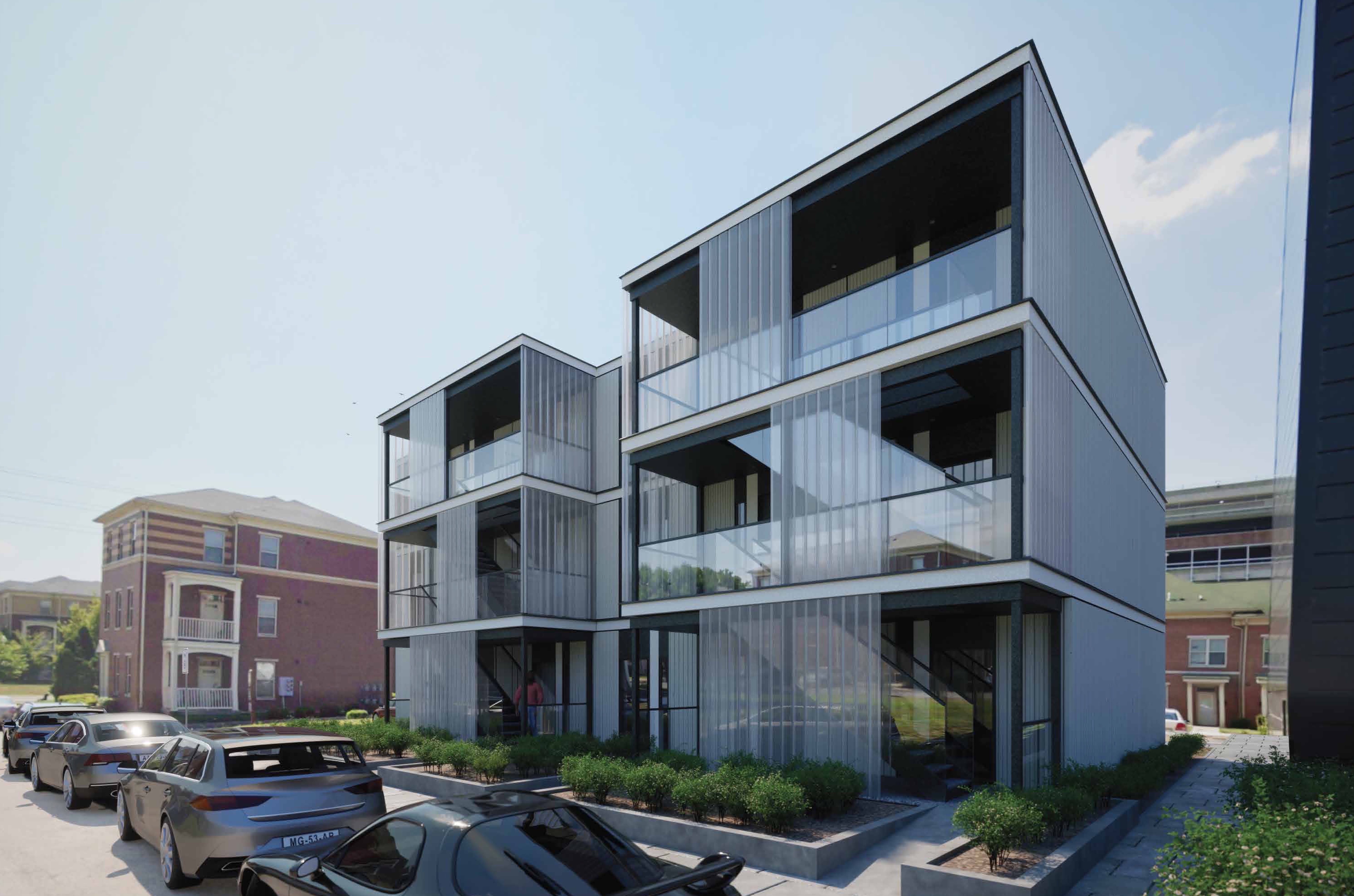
Accelerated development
Increase your development output by reducing your project timeline to 16 weeks from start to finish with much greater time & cost certainty.
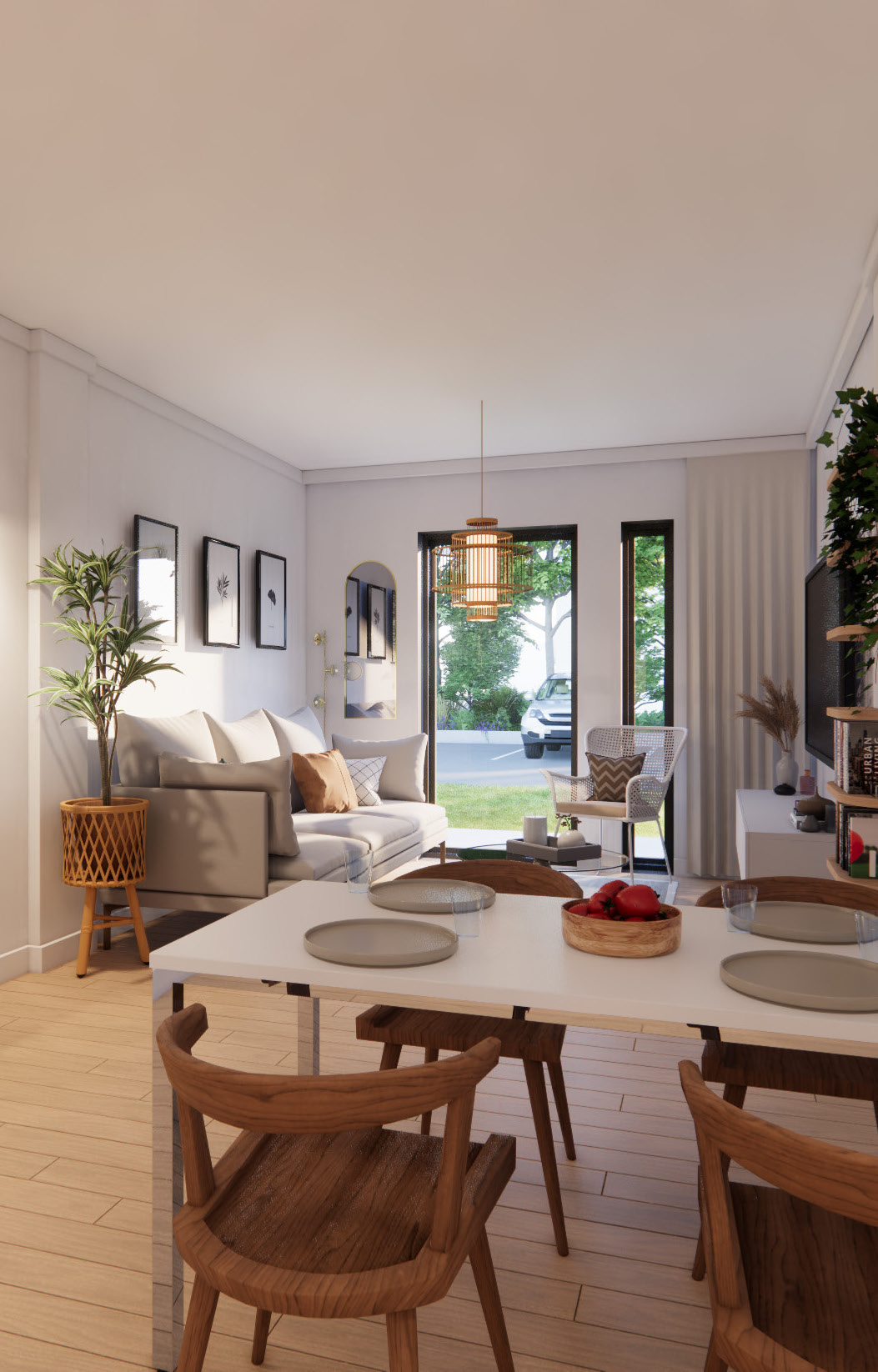
High quality
Completed units not only meet but exceed local building codes and standards, outperforming traditionally constructed homes. This results in high-quality housing stock and reduced ongoing operational and maintenance costs.
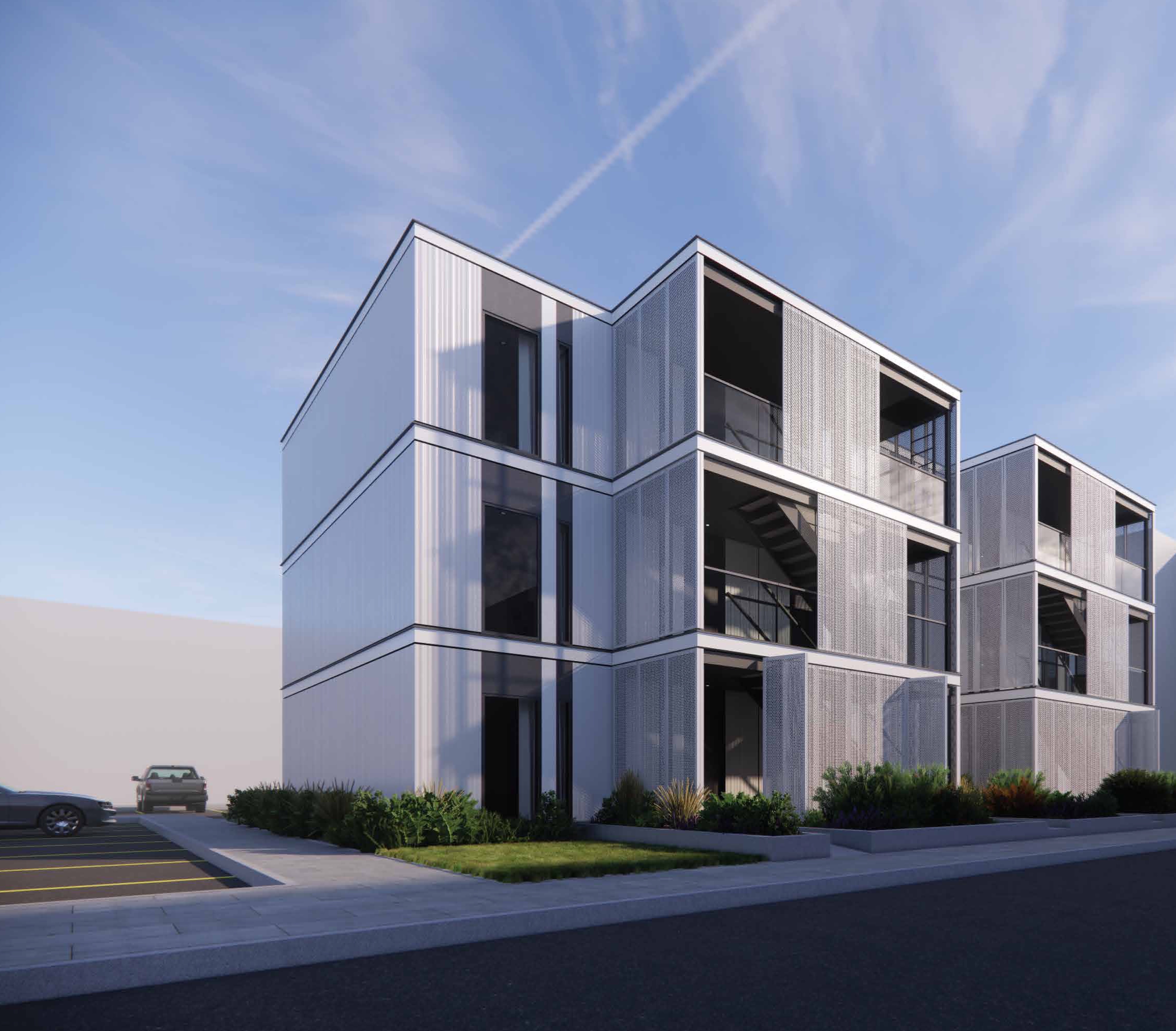
Highly scalable
Due to the repeatability of our system, you can repeat commercially successful projects across your land bank.
The Multiplex has benefits beyond being faster, more accurate & more sustainable
70% fewer site workers
Labour requirement are fewer in total and offsite labour can now be serviced in more attractive working conditions.
90% fewer accidents
All work is performed at the ground level with weather protection, resulting in extremely safe work conditions.
Full control
Digital records of all manufacturing and on-site work are integrated into a building digital twin, providing complete visibility of the development process and traceability of finished apartments.
Mold free
The high-precision construction method and selection of high-performance materials ensure that units remain free from mold.
How it works
Multiplexes are permanent units consisting of modules made off-site.
Choose your Development Size
Choose your development's width and height to suit your site and local site planning requirements. The Multiplex can go up to 8 storeys and as wide as you want.
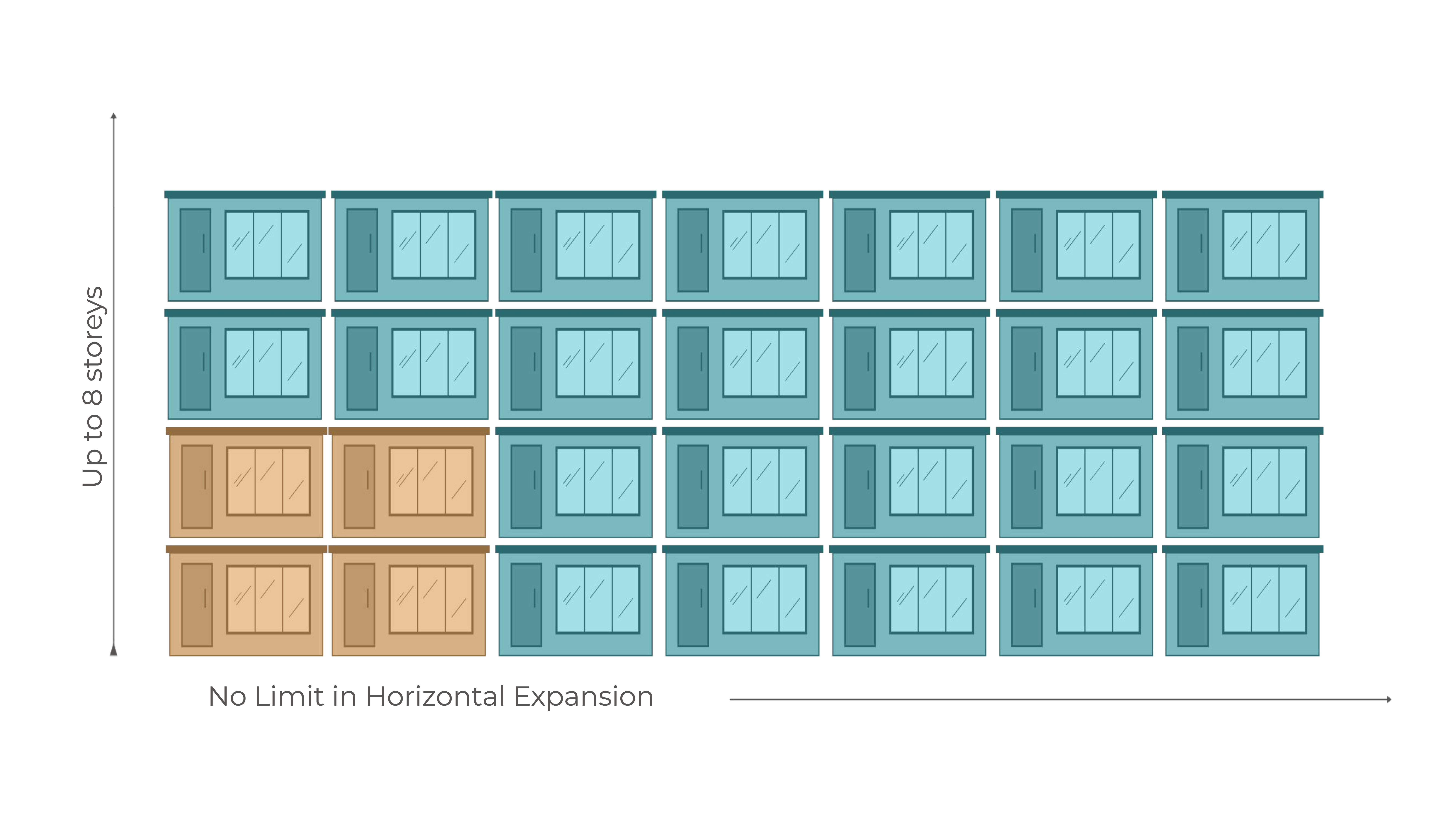
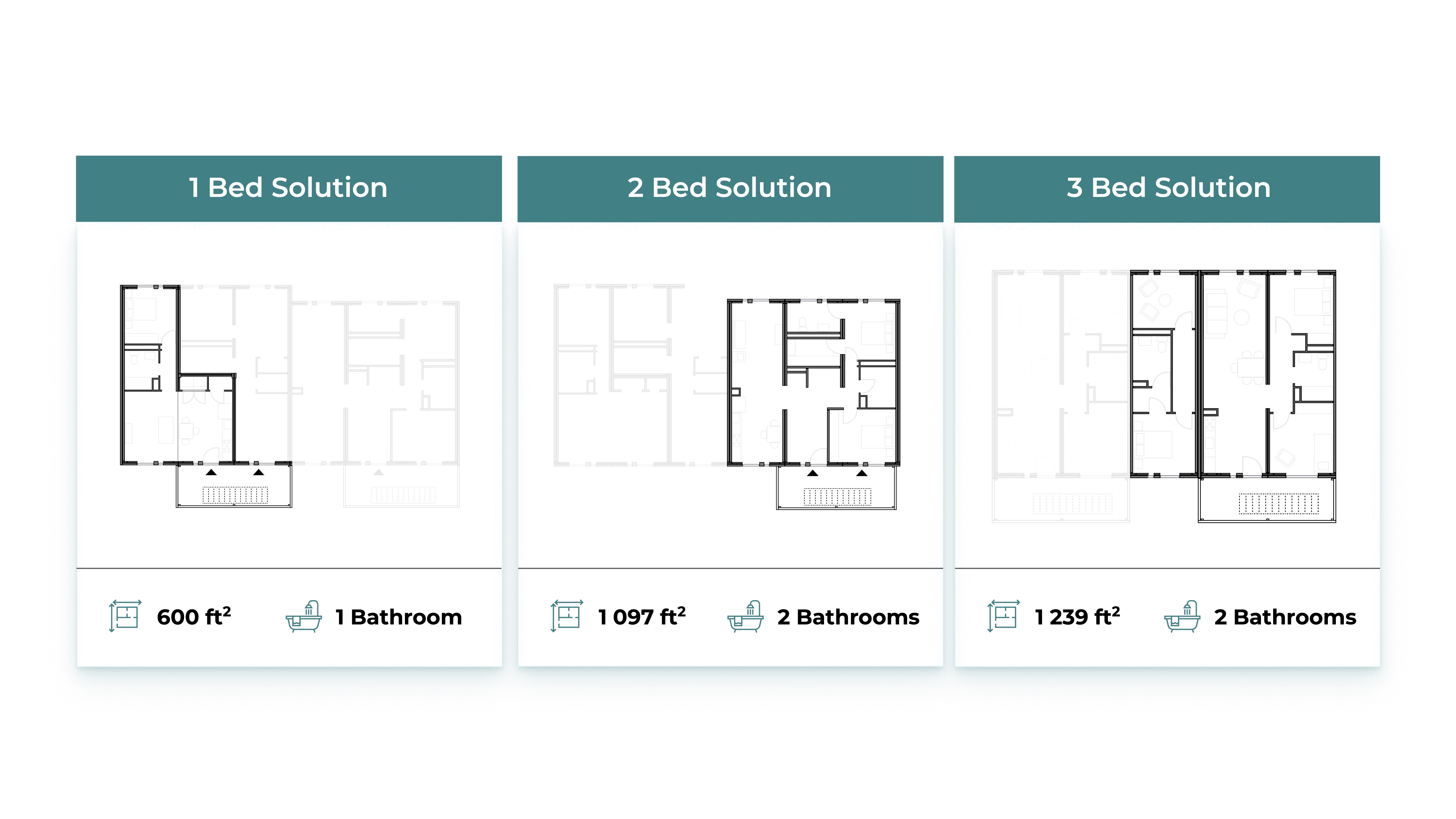
Choose your Unit Mix
Configure your development using our range of permit-ready Multiplex unit plans to create the unit mix you would like. Our range includes designs for studio's, one-bedrooms, two-bedrooms and three-bedrooms. This dramatically reduces your design cost and timeline.
Choose your Style
Choose from a range of standardized facade designs to suit your built environment.
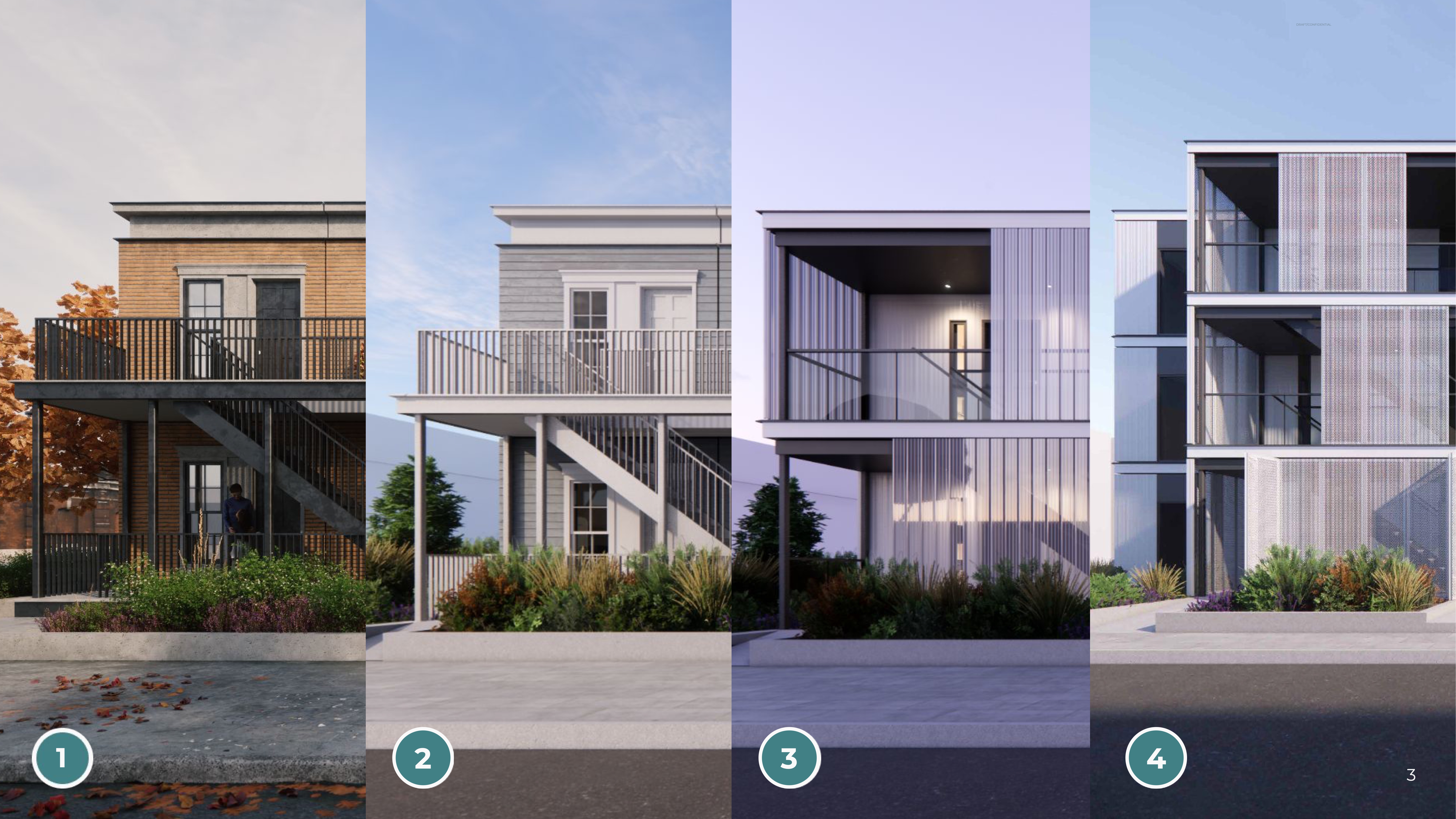
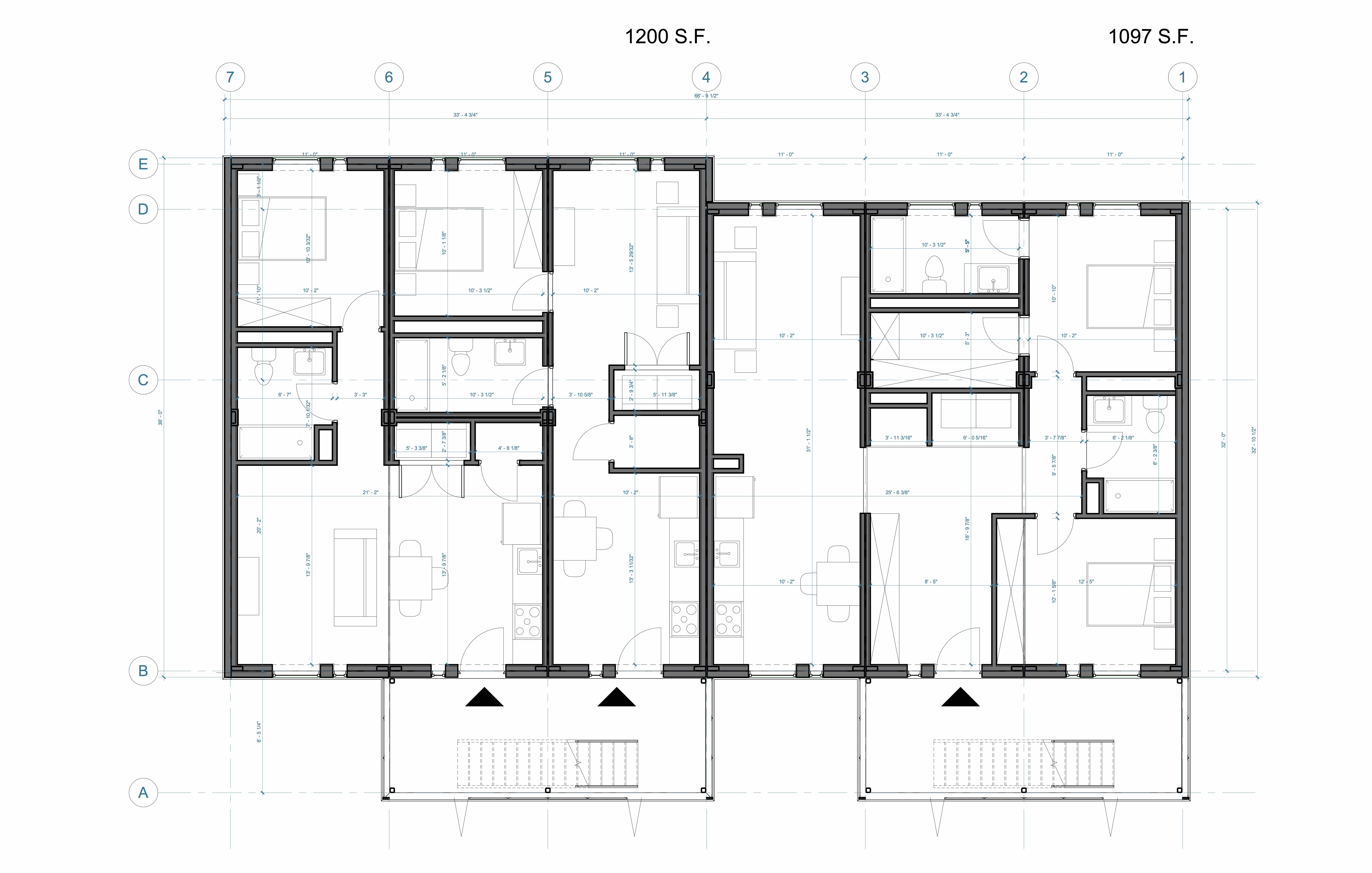
Approve your Detailed Design
Our multiplex units are pre-engineered to comply with building codes across 47 U.S. states. Once you provide the final approval, MMY US will handle the submission of these plans to the relevant state authority in your area to secure the building permits.
We manufacture your apartments
MMY's Multiplexes are pre-fabricated in a factory as complete modules, encompassing structure, MEP systems, furniture, fixtures, and both interior and exterior finishes. Our proprietary cold-formed steel system boosts off-site labor efficiency in modular construction from 60% to 85%, inclusive of pre-cladding.
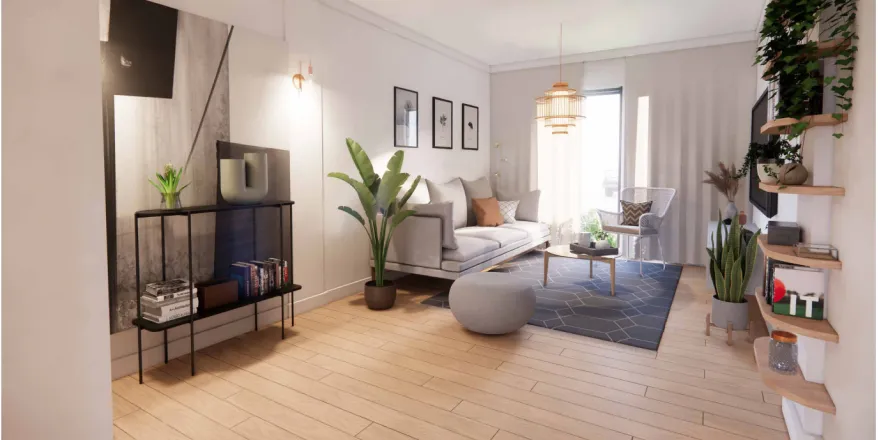
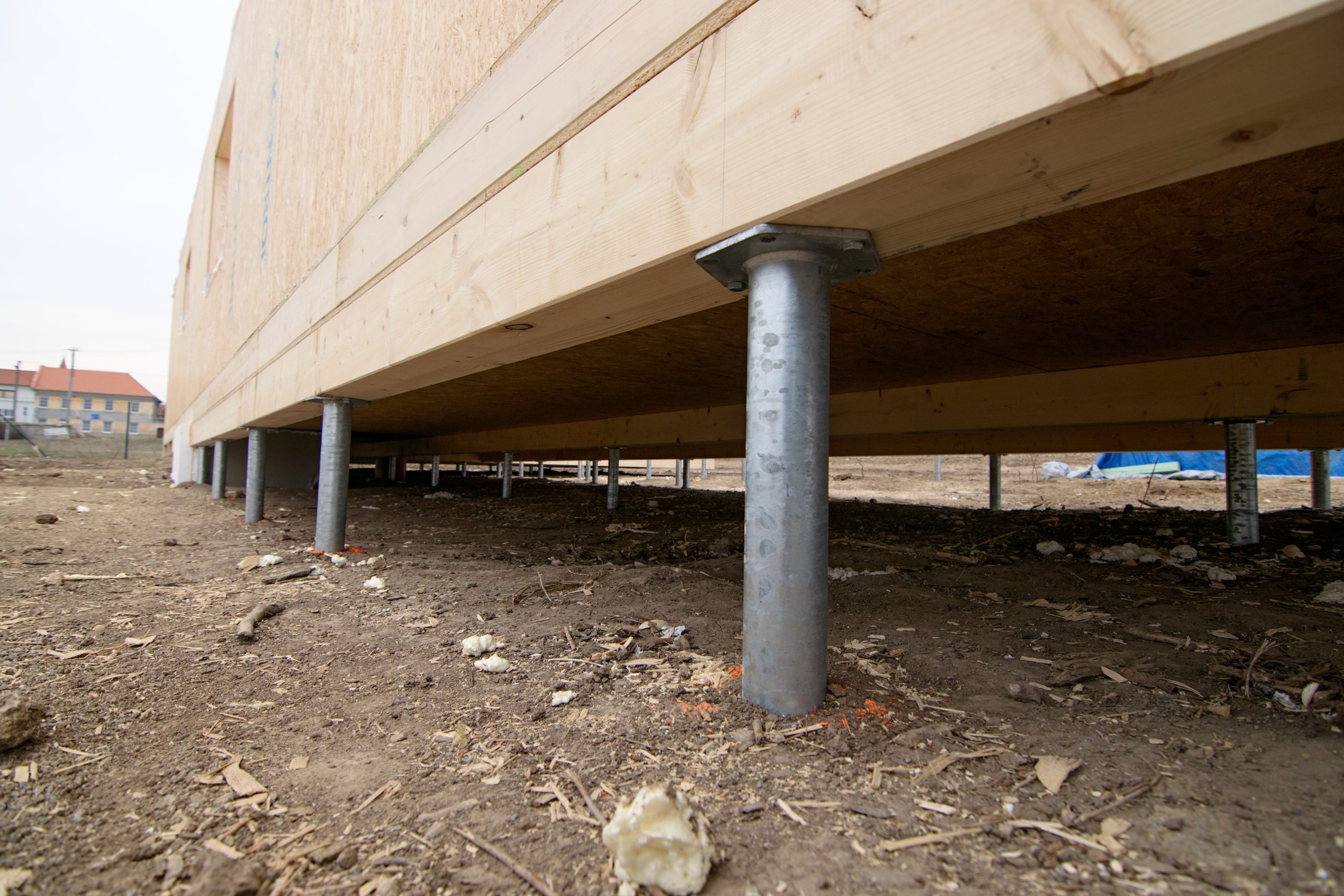
We perform your site works
While the appropriate foundation ultimately depends on the site, MMY's intramodular connection system is compatible with helical ground screws, eliminating the necessity for costly, time-consuming, and carbon-heavy concrete foundations.
We transport the modules to site
We transport the modules to site. Our unique chassis design enables nationwide rail transport from a single facility at minimal cost, allowing you to develop Multiplexes anywhere, unrestricted by factory proximity.
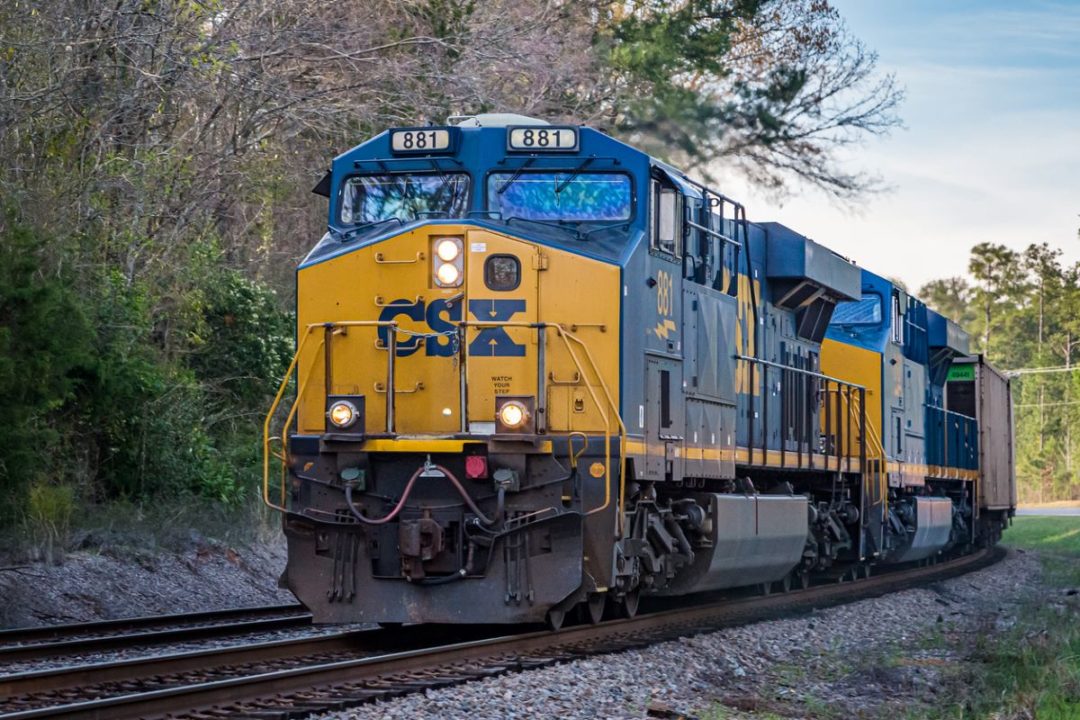
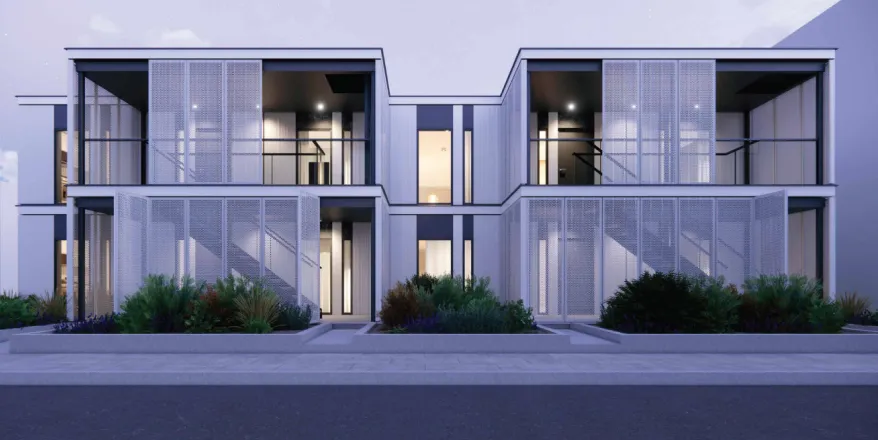
Install & Handover!
In just a few days, we set, connect and zip the modules, forming the complete building structure. Our modular structures meet all traditional building codes. After completion, we promptly sign off and hand over your development!
Quadplex
Sixplex
Eightplex
Twelveplex
Eighteenplex
Customize your Multiplexes with our selection of pre-designed, pre-engineered units for streamlined configuration.
For example, a Quadplex
Build Multiplexes from 4 to 60 units per structure.
One system. Lots of facades.
Choose from 4 different standardized facade designs to suit your built environment.
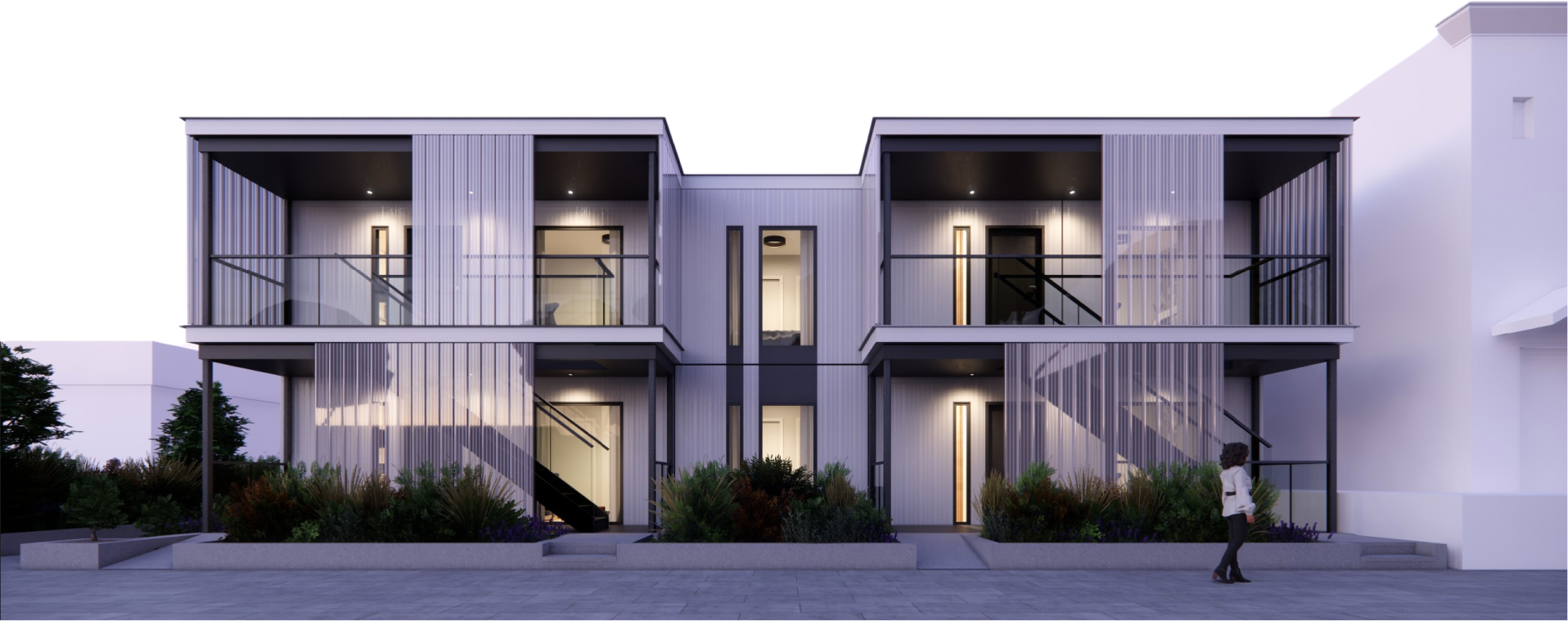
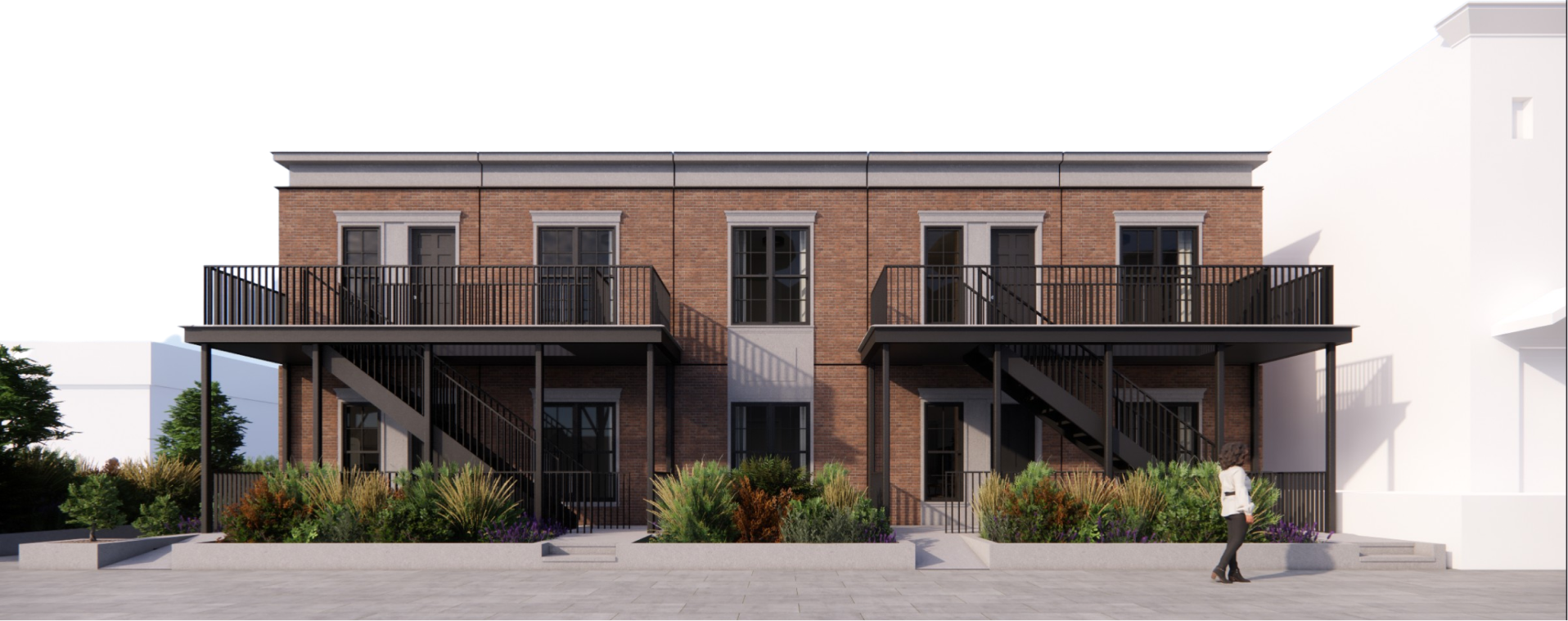
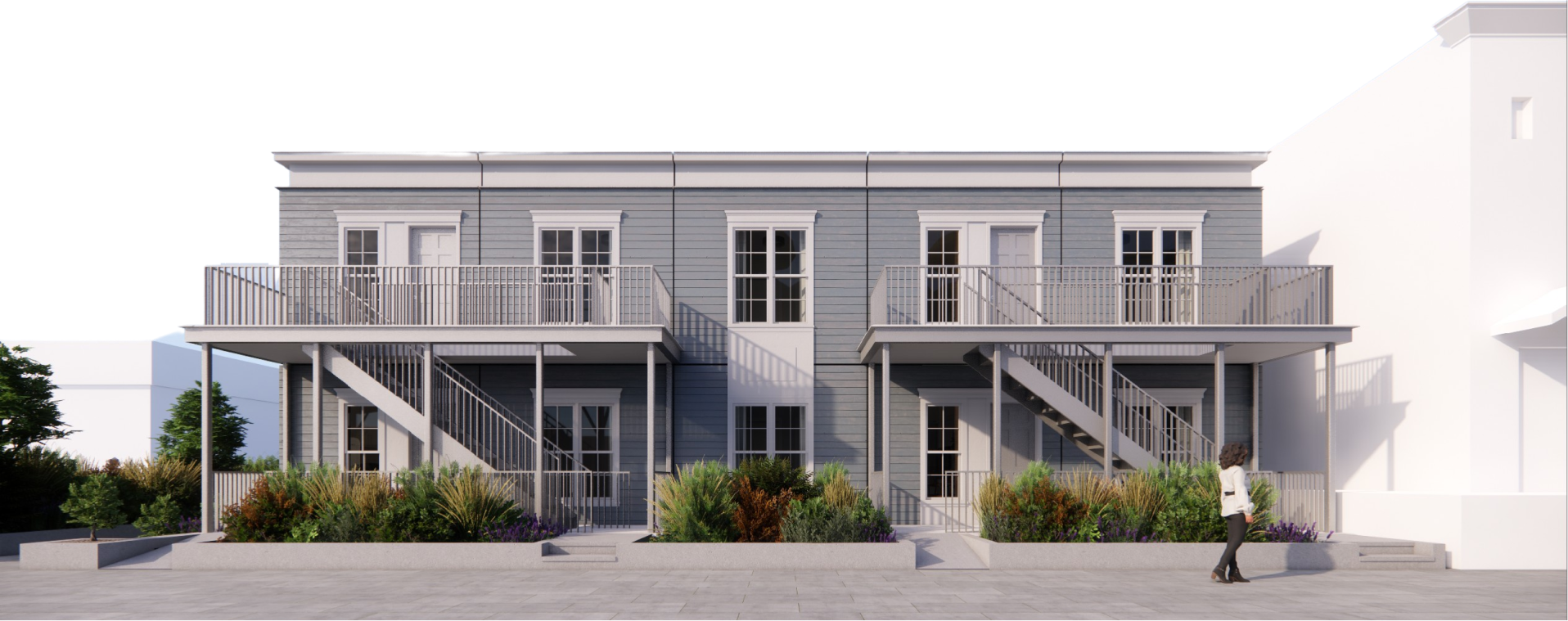
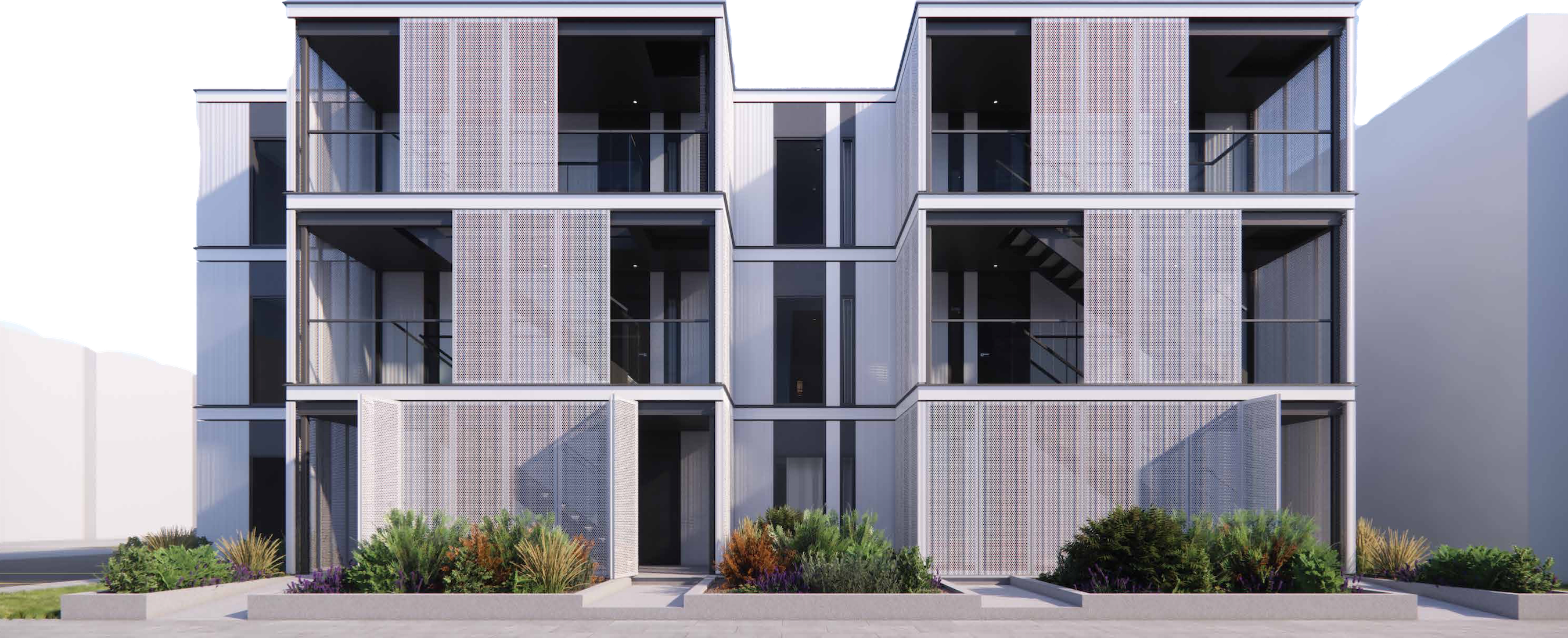
Interiors
Every unit comes fully finished with a high quality fitout.
Each module comes fully completed with structure, MEP & interior finishes
Project timeline
Multiplexes are permanent units consisting of modules made off-site.
Tailoring your Multiplex
Multiplexes can be configured from a mixture of pre-designed permit-ready units.
1 bedroom solution
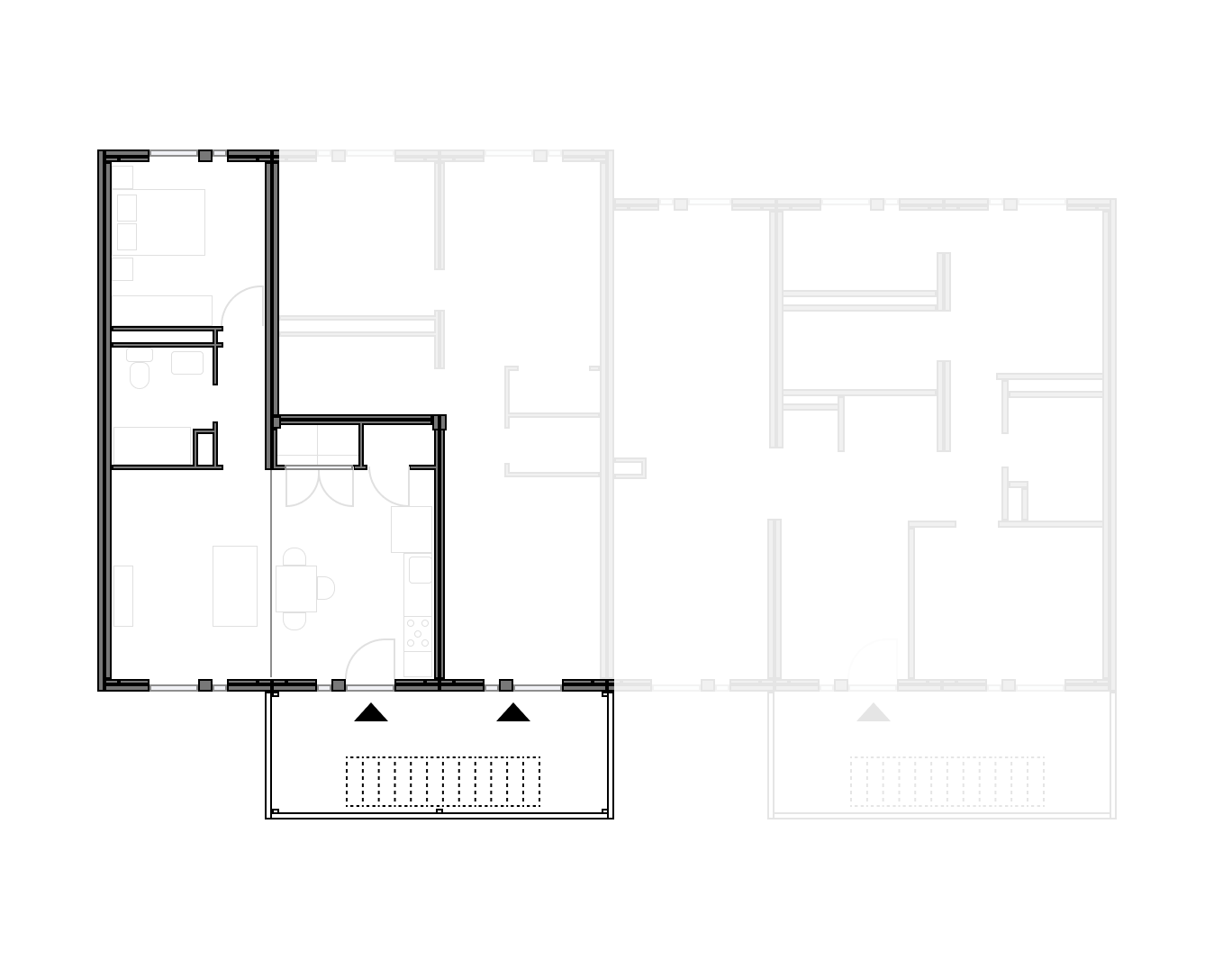
2 bedroom solution
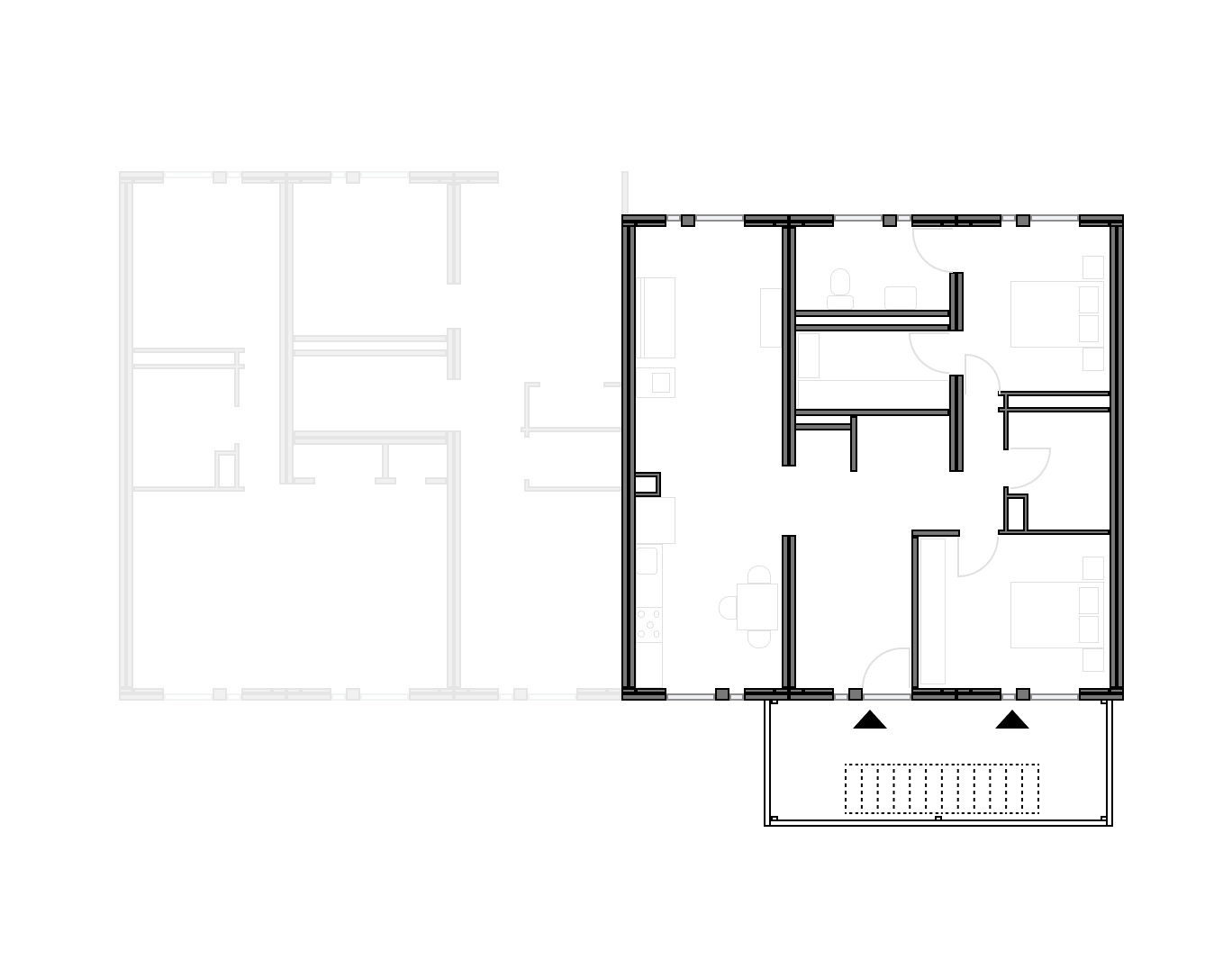
3 bedroom solution
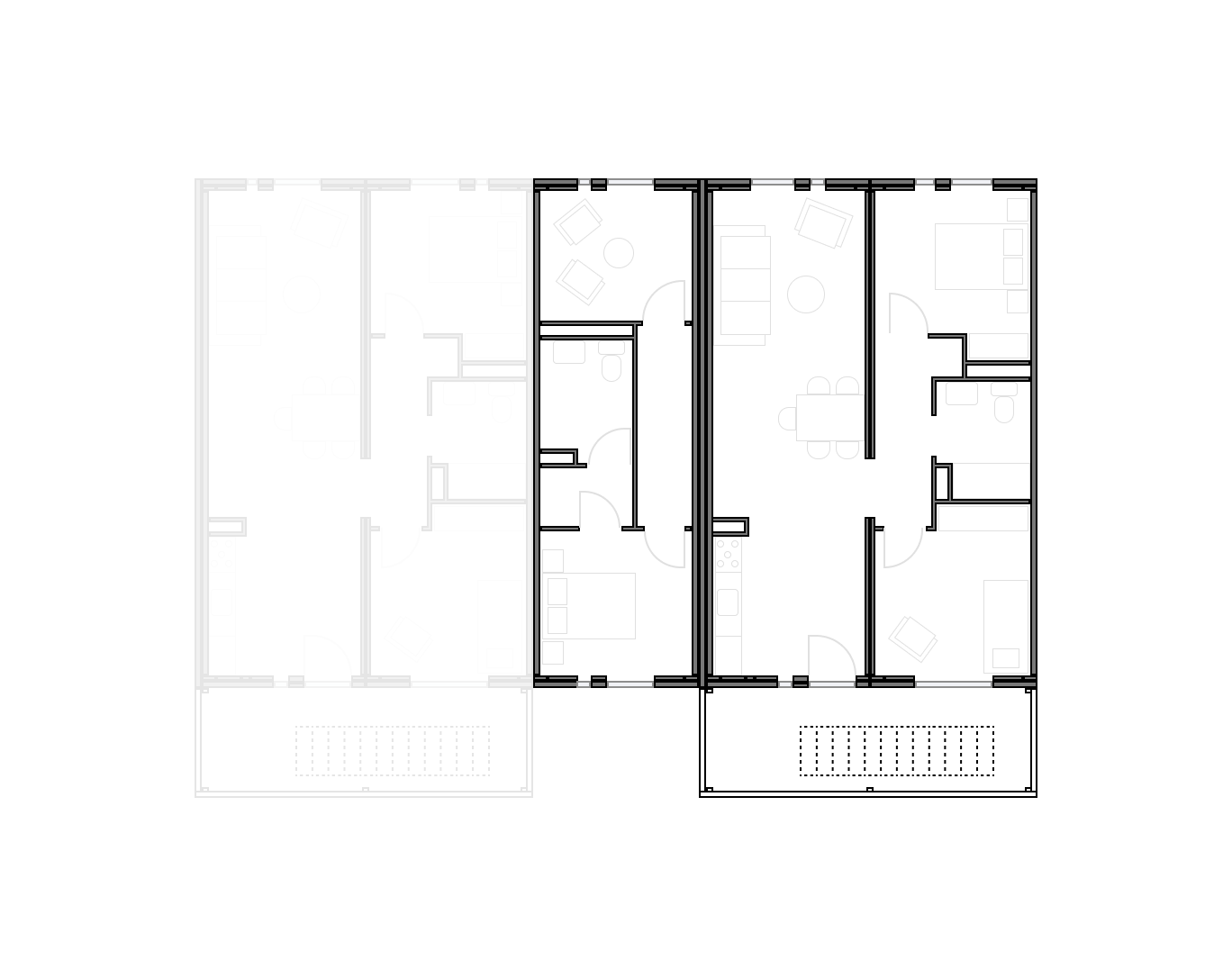
Trusted by leaders
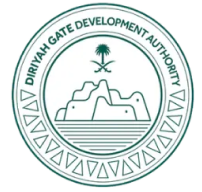
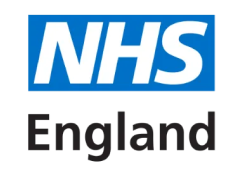
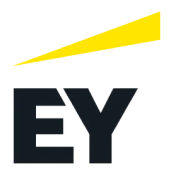
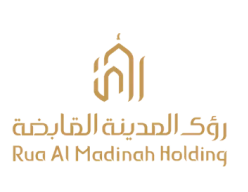
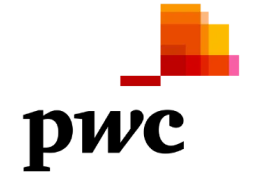
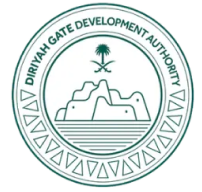
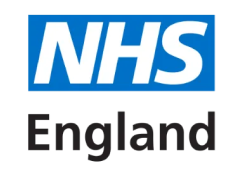
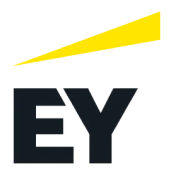
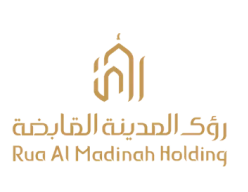
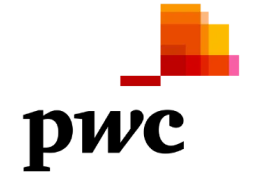
Kentucky developers are excited to build faster
"Wow, I am extremely impressed and would like to continue the discussion of working together. What are the next steps?"
"They are beautiful! Let's discuss tomorrow in more detail how we can use these in the two projects we discussed."
"I think the information you shared at the meeting was phenomenal. I would love to speak with you further about your model."
"I am so very excited to hear that you are so close to up and running. The city will be a great partner to MMY as we move forward to fill our housing gaps!"
"Wow, I am extremely impressed and would like to continue the discussion of working together. What are the next steps?"
"They are beautiful! Let's discuss tomorrow in more detail how we can use these in the two projects we discussed."
"I think the information you shared at the meeting was phenomenal. I would love to speak with you further about your model."
"I am so very excited to hear that you are so close to up and running. The city will be a great partner to MMY as we move forward to fill our housing gaps!"
Frequently asked questions
What is modular construction, and how does it differ from traditional construction methods
Modular construction involves constructing building modules in a factory setting and then transporting them to the construction site for assembly. It differs from traditional methods where construction is done entirely on-site. This approach allows for more controlled manufacturing conditions, leading to efficiency and quality improvements.
What are the environmental benefits of modular construction?
The MMY Multiplex offers significant environmental advantages, notably a 35% reduction in carbon emissions compared to traditional construction. This translates to an average decrease of 32 tons of CO2 per unit, showcasing a more sustainable approach to construction.
How long does it take to build a modular home, and is it faster than traditional construction?
Building a Multiplex takes approximately 16 weeks from approval to completion, significantly faster than the average 76 weeks required for traditional multifamily developments in the US. This means the Multiplex system can accelerate the development process by about 5 times, thanks to its innovative cold-formed steel system.
What is the cost comparison between modular and traditional construction?
The MMY Multiplex system offers cost advantages over traditional construction. Its repetitive design significantly lowers per unit costs by eliminating extra architectural and engineering expenses for repeated developments. Additionally, for orders above 100 units, developers can enjoy 15-35% lower development costs compared to traditional methods, thanks to volume discounts. This makes the MMY Multiplex system cost-effective, especially for large-scale or multiple projects.
Do modular homes meet local building codes and regulations?
Modular homes, including those built using the MMY Multiplex system, meet the same local building codes and regulations as traditionally built housing. The difference lies in the construction process, not in the compliance or quality standards.
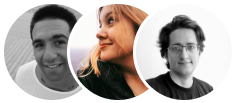
Still have questions?
Can’t find the answer you’re looking for? Please chat to our friendly team.
Help us to improve
Please take a moment to share your thoughts, suggestions, or concerns about the product, website or anything else.